

Used to maintain temperature of a product within a tank (or to prevent hot external surfaces). Furphy Engineering manufacture stainless steel tanks for a number of industries including Dairy, Brewing, Chemical, Energy, Mining, Industrial, Food & Beverage, Pulp & Paper, Water & Environment, Wine, Galvanizing, Pharmaceutical This is conducted by filling the vessels with water to a level to achieve a calculated test pressure as per AS1210. This is a method of testing our stainless steel pressure vessels for both strength and leaks. This method is used when large volume of medium is present or when a substantial change in temperature is required. This is then used to pump a heating medium through to control the temperature of the product within the vessel.

#PRESSURE VESSEL AGITATOR DESIGN SERIES#
This process involves immersion of steel into molten zinc to produce a coating of zinc-iron alloy.Ī chart with a series of horizontal lines used to plan and display the amount of production completed over time in relation to the amount planned for the project.Īn external heat exchanger in which a half (cross-section) of pipe is rolled around and welded to the eternal tank surface. General Arrangement (Engineering Drawing).Ī surface protection coating applied to carbon steel to provide long term corrosion protection. This is used for bolting or connecting various fittings or other pipes. These will generally house or connect to instrumentation or pipe work and facilitate the operation of the vessel.Ī plate or ring used to form a rim at the end of a pipe when fastened or welded to the pipe. High Chromium and Molybdenum contents give excellent corrosion resistance and the microstructure gives high strength and resistance to stress corrosion cracking.Īny nozzle, protrusion or opening in a tank or vessel. Most common is 2205 grade (UNS S31803 and/or UNS S32205). Stainless steel that has the properties of both austenitic and ferritic steels. These are formed Furphy Engineering by cold pressing (dishing) a circular plate, before roll forming a “knuckle” at the outside perimeter to enable to join and butt weld to a vessel strake. Commonly used where the design requires more strength than can be achieved with a cone or flat end.
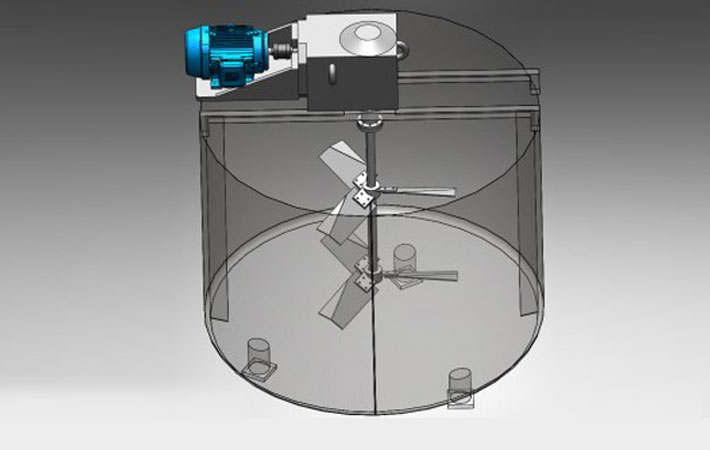
Heating or cooling medium can then be pumped through this cavity to maintain the temperature of the product within the tank.Įnd cap on a cylindrically shaped vessel incorporating a dish with a fixed radius.
#PRESSURE VESSEL AGITATOR DESIGN SKIN#
The fixed radius of a dished head or dished end.Ī method of heat transfer where a thin, stainless steel skin is formed and affixed to the external of a tank shell with spot welds located in a regular “dimple” pattern, in order to create cavity between the second skin and the external tank wall. The material used can be carbon steel, aluminium or stainless steel of various profiles to suit the given application. The outer casing of a tank or vessel that is made from material generally 1.0mm material and of a riveted construction. BSM fittings are tightly fastened and require tools to remove and retighten. Our tank nozzles will often be a length of tube with a BSM male part welded to the end, to enable connecting the tank to a tube line in the overall process.

This can be done smoothly or vigorously to suit the required product and process.Īmerican National Standards Institute – Pipe flanges and flanged fittings.Īmerican Petroleum Institute – Welded tanks for oil storage.Īustralian Standard – Fixed platforms, walkways, stairways and ladders – Design, construction and installation.Īustralian Standard – Steel tanks for flammable and combustible liquids.Īustralian Standard – Flanges for pipes, valves & fittings.Īustralian Standard – Pressure equipment – Welding and brazing qualification.Īustralian Standard – Pressure equipment – Hazard levels.īill Of Materials this is a compiled list of all materials required in the manufacture of a tank or vessel.īSM (British Standard Milk) Unions are sanitary and hygienic stainless steel tube couplings which consist of a nut, liner male part and o-ring. Slightly different grades of 304 and 316 stainless steel that have lower levels of carbon content and is used in applications where sensitisation corrosion might occur in welded components.Ī mixer or stirrer fitted to a tank in order to move or blend the contents in the tank. These flanges came in a number of different pressure ratings. And the ‘RF’ identifies the face of the flange which is a Raised Face (RF) in this case. The 150# is a number used to identify the pressure rating of the flange (In this case 150 lbs). Often described as marine grade due to its higher corrosion resistance. 316 offers a higher corrosion resistance than grade 304 with higher content of nickel. The most common form of stainless steel used in tank and pressure vessel manufacture.
